
Measuring Effectiveness – KPIs
In Lean management, measuring effectiveness plays a crucial role. To achieve success in this approach, it is essential to precisely define and monitor Key Performance Indicators (KPIs). Lean focuses on identifying potential, areas for improvement, and continuously monitoring progress. KPIs serve as indicators that enable an accurate assessment of whether the company is moving towards optimal resource utilization and waste minimization. The role of KPIs in operational excellence involves closely tracking process efficiency, identifying areas that require attention, thereby allowing for the elimination of inefficiencies. Through the measurement of KPIs, a company becomes more flexible and prepared to quickly adapt to changing market conditions.
Table of contents
- Why measure Lean effectiveness?
- KPIs in Lean Management – The Key to Effective Monitoring
- Categories of Key Performance Indicators
- The process of implementing Key Performance Indicators (KPIs) in a company
- Technologies Supporting Lean Efficiency Monitoring
- Summary
1. Why measure Lean effectiveness?
Measuring effectiveness in the context of Lean management is a key element of strategic process improvement. Without a precise assessment of progress, effectively eliminating waste becomes challenging. Therefore, understanding the goals of measuring effectiveness is crucial.
The first goal is to accurately identify where and why losses occur. Key Performance Indicators (KPIs) act as a ‘magnifying glass,’ providing a detailed look at specific operational areas. This allows the identification of specific areas that require improvement, which is crucial for effective process improvement. Instead of acting broadly, a company can optimize specific elements that have the greatest impact on efficiency.
Another significant aspect of measuring effectiveness is employee motivation. When employees see the direct impact of their work on indicators, they begin to make more informed decisions and engage in the improvement process. Understanding that their efforts translate into measurable results stimulates engagement and creates an organizational culture conducive to continuous improvement.
Finally, effective measurement of effectiveness enables a company to quickly respond to market changes. Identifying issues in real-time allows flexible adaptation of strategies and avoids delays in operational improvement. Dynamic adjustment to the changing business environment becomes a key competitive advantage.

2. KPIs in Lean Management – The Key to Effective Monitoring
Effective management requires precise monitoring of Key Performance Indicators (KPIs), which serve as barometers of process status. The key objective is to select appropriate KPIs tailored to the specific characteristics of the company’s operations. These guidelines act as lighthouses, casting light on areas that require attention.
- Selecting Appropriate KPIs for Processes
It is crucial to align KPIs with the nature of the business. For manufacturing processes, quality indicators such as defect levels or compliance with standards are essential. In office areas, key performance indicators for process efficiency, including cycle time, are crucial. Additionally, measuring costs, both in production and potential waste, is an important aspect.
- Impact of KPIs on Waste Elimination
Precise KPIs help identify areas of waste. Quality indicators facilitate pinpointing error sources, while process efficiency indicators help identify delays and downtimes. Cost-related KPIs enable the analysis of where investments in waste elimination will yield the greatest benefits. As a result, the improvement process becomes focused, efficient, and swift.
- Role of KPIs in Operational Excellence
KPIs play a crucial role in the continuous improvement process. Indicators serve as a data source for analysis, enabling informed decisions regarding improvement strategies. When a team sees the specific impact of their work on a chosen KPI, it fosters motivation to engage in the improvement process. This role is not just about control but primarily about inspiration.
- Examples of Key Performance Indicators
Successful KPI implementations include reducing defects by a certain percentage within a month or shortening production cycle time. Human resource indicators, such as employee engagement levels, are also crucial for monitoring. These examples illustrate how KPIs can shape and accelerate the operational improvement process.
3. Categories of Key Performance Indicators
Categories of KPIs form a comprehensive performance measurement system, allowing for a holistic view of the company’s operations. Introducing Lean Management in each of these categories requires diligence and adaptation to the industry’s specifics. Effective monitoring of each of these areas enables the precise identification of areas for improvement, which is crucial for efficient Lean management. The goal is not only to minimize waste but also to achieve operational excellence in every aspect of the company’s operations.
Quality Indicators
In this category, the focus is on the quality of products or services. The defect rate is a key indicator, allowing an assessment of whether the production process generates faulty units. Additionally, indicators of compliance with quality standards are crucial to ensure that the company meets industry standards and customer expectations.
Process Efficiency Indicators
Operational efficiency often depends on the performance of individual processes. Process cycle time indicators allow an assessment of how much time a particular stage takes, potentially identifying areas of delay. Labor efficiency indicators measure the operational effectiveness of employees, which is crucial for process optimization.
Cost Indicators
Cost analysis is an important element of Lean Management. Production cost indicators allow monitoring of the effectiveness of actions, identification of areas where costs are highest, and the search for potential waste. Indicators related to waste costs are also extremely important, enabling the identification and elimination of sources of loss.
Customer Indicators
Customer satisfaction is a key element of the company’s success. Indicators in this category include customer satisfaction levels, delivery times, and potential complaints. This data reflects not only the quality of products but also the speed and flexibility of the company in responding to customer needs.
Human Resources Indicators
Operational efficiency is also tied to employee engagement. Human resources indicators include employee engagement levels, organizational climate assessments, and absenteeism indicators. Understanding these aspects allows for effective personnel management and the creation of working conditions conducive to process improvement.
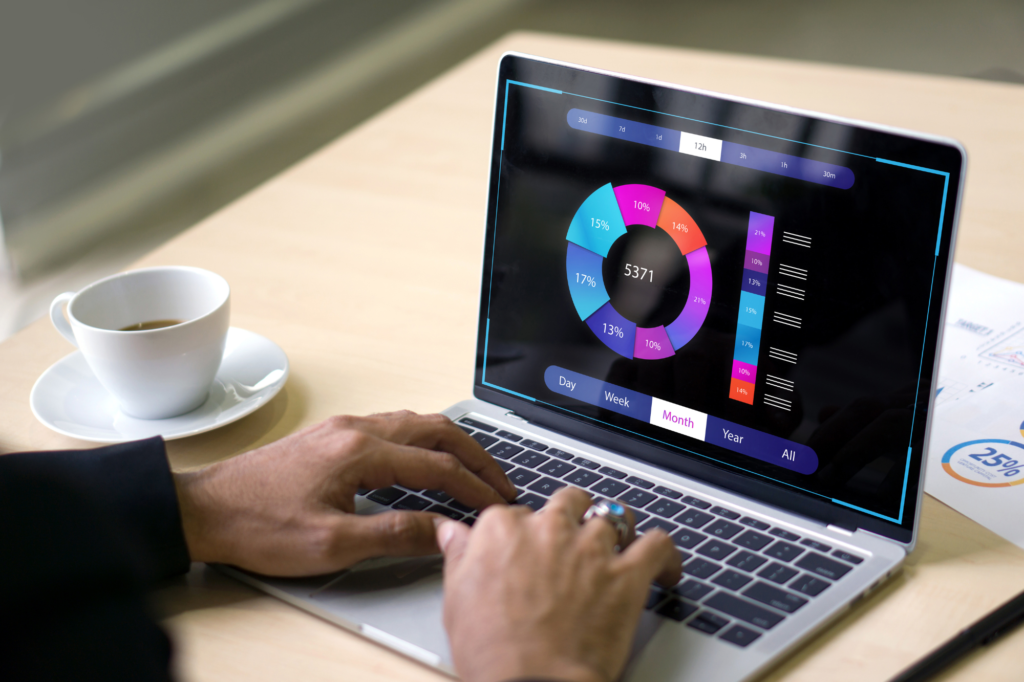
4. The process of implementing KPIs in a company
The process of implementing Key Performance Indicators (KPIs) in a company requires not only a thorough understanding of the organization’s goals but also precise alignment of KPIs with the industry and operational specifics of the company.
The first step is identifying key areas for operational efficiency. For a manufacturing company, these might be quality and production efficiency indicators, while a service-oriented company may focus more on customer service indicators. It is crucial for KPIs to be measurable, achievable, and directly related to the company’s strategic goals.
Implementing KPIs involves not only choosing the right indicators but also creating a monitoring system, collecting data, and analyzing results. It is necessary to adjust information systems for data collection and prepare staff for regular reporting. Investing in data analysis training is also valuable to enable the team to interpret results effectively.
However, implementing KPIs may face various challenges, such as employee resistance to a new measurement system or a lack of resources for effective monitoring. It is important for the management to be prepared for effective change management, providing the necessary support and motivating employees to engage.
The implementation of KPIs is a dynamic process that requires constant monitoring and adjustments. As data is collected, the company should actively analyze results and take corrective actions when indicators point to potential issues. It is a continuous improvement loop that allows adaptation to changing market and organizational conditions.
5. Technologies Supporting Lean Efficiency Monitoring
Implementing modern technological tools not only facilitates data collection but also supports analysis, interpretation, and quick response to changing business conditions.
Technologies enable the automation of data collection, eliminating human errors and increasing measurement accuracy. Automation allows for continuous monitoring of selected KPIs, which is particularly crucial in areas where a rapid response to changing conditions is key.
The introduction of Business Intelligence (BI) systems is a step towards more advanced data analysis. These systems enable the collection, processing, and visualization of data, making it easier to understand trends and identify areas for improvement. BI becomes an integral tool for companies aiming for effective KPI management.
Internet of Things (IoT) technologies introduce new possibilities for real-time monitoring. IoT sensors and devices enable the tracking of production processes, monitoring machine conditions, or workplace environments. This means that data is not only collected at specific moments but continuously, allowing for ongoing analysis and quick responses to potential issues.
Big Data analysis is also a crucial tool. Large amounts of data can be analyzed to uncover hidden patterns, leading to a better understanding of processes and the ability to identify areas for optimization. Advanced data analysis algorithms support fact-based decision-making.
Enterprise Resource Planning (ERP) and Customer Relationship Management (CRM) systems should also be considered. These systems provide comprehensive solutions for managing processes within a company. Integrating these systems with KPIs allows for a fuller understanding of the impact of operational activities on customer relationships and the overall efficiency of the company.

6. Summary
In summary, measuring effectiveness through Key Performance Indicators (KPIs) not only allows a company to precisely identify areas for improvement but also becomes a crucial motivational tool for employees. The implementation of KPIs is a dynamic process that requires continuous monitoring, adaptation, and response to changing market conditions. Introducing technologies such as automation, Business Intelligence (BI) systems, or the Internet of Things (IoT) further supports effective Lean management, providing companies with the ability to quickly respond to changes and achieve operational excellence.