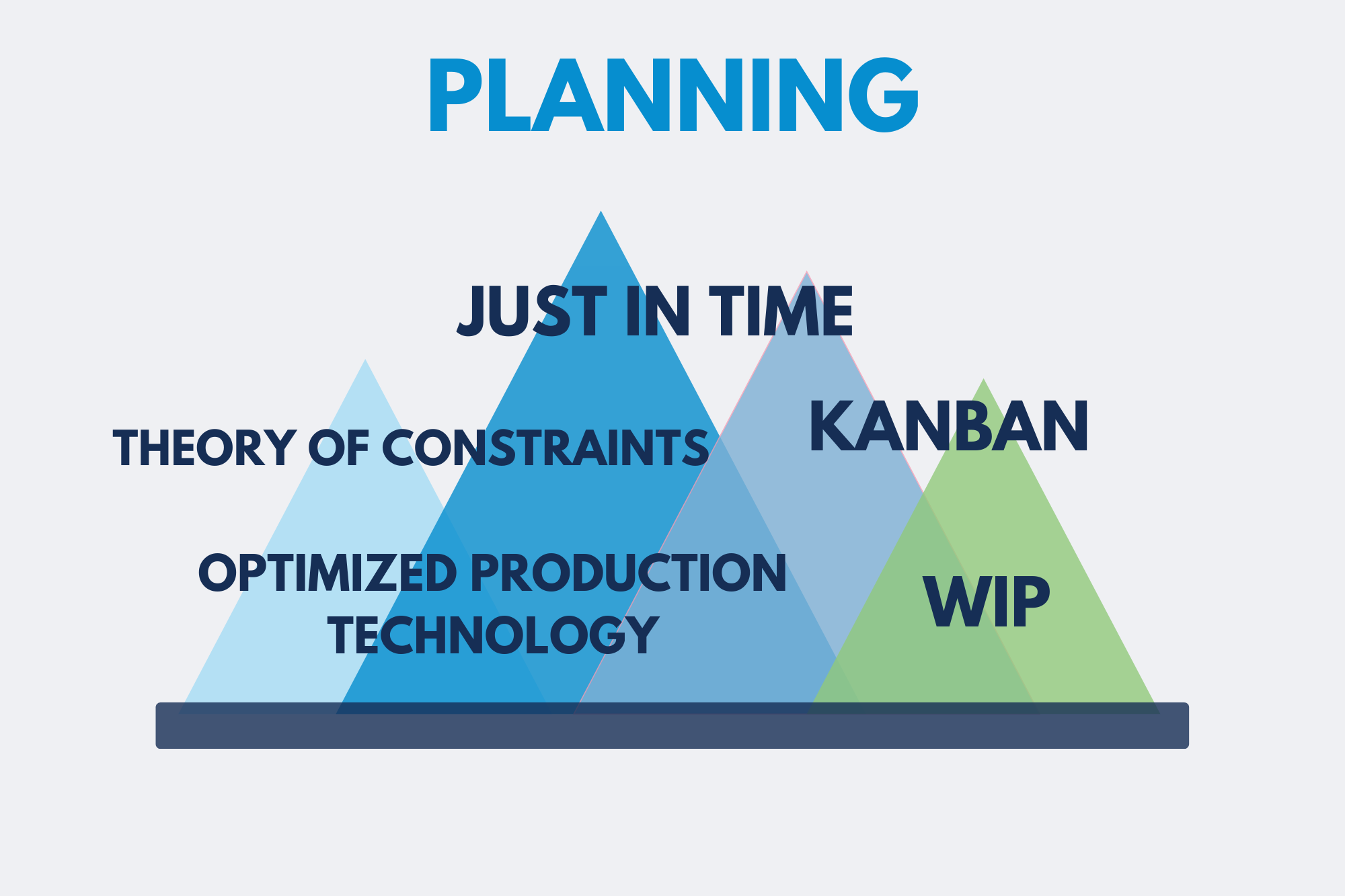
What do you need to know to plan well?
Good planning is a key aspect of the proper functioning of any enterprise, just like communication. It enables cost optimization, which supports the overall financial performance of the organization. Its significance lies in the ability to streamline the decision-making process, improve efficiency, and facilitate the achievement of objectives.
Market requirements, particularly the increasing demand for diverse products, short production series, and the short product life cycle, make the ability to react quickly and accurately to market needs crucial for competitiveness in the modern market. The concept of lean production focuses the enterprise’s activities on handling the production order by integrating individual functions of the company precisely as required for order fulfillment. It is characterized by producing just the quantity that the customer demands at any given moment.
Table of contents
- Stages of planning
- Basic planning techniques
- Types of pull planning
- Types of event-oriented planning
- Summary
1. Stages of planning
1.1 Goal identification – clear definition of what we want to achieve.
1.2 Situation analysis – analysis of internal and external factors that may impact goal achievement. Internal analysis focuses on the organization’s resources, strengths, and weaknesses, while external analysis includes factors such as market environment, competition, social, and political trends.
1.3 Strategy formulation – it should encompass specific actions to leverage organizational strengths, address weaknesses, capitalize on opportunities, and mitigate threats arising from the environment.
1.4 Defining specific goals – related to the overall strategy, they should be measurable, time-defined, and aligned with strategic goals.
1.5 Selection of means and resources – this may involve choosing appropriate technologies, allocating the right teams, and financial resources.
1.6 Developing action plans – development of concrete plans that are coherent, flexible, and consider various possible scenarios.
1.7 Implementation and control – implementation of developed plans and systematic monitoring of progress to track achievements. If necessary, adjustments to plans and strategies may be made through corrections.
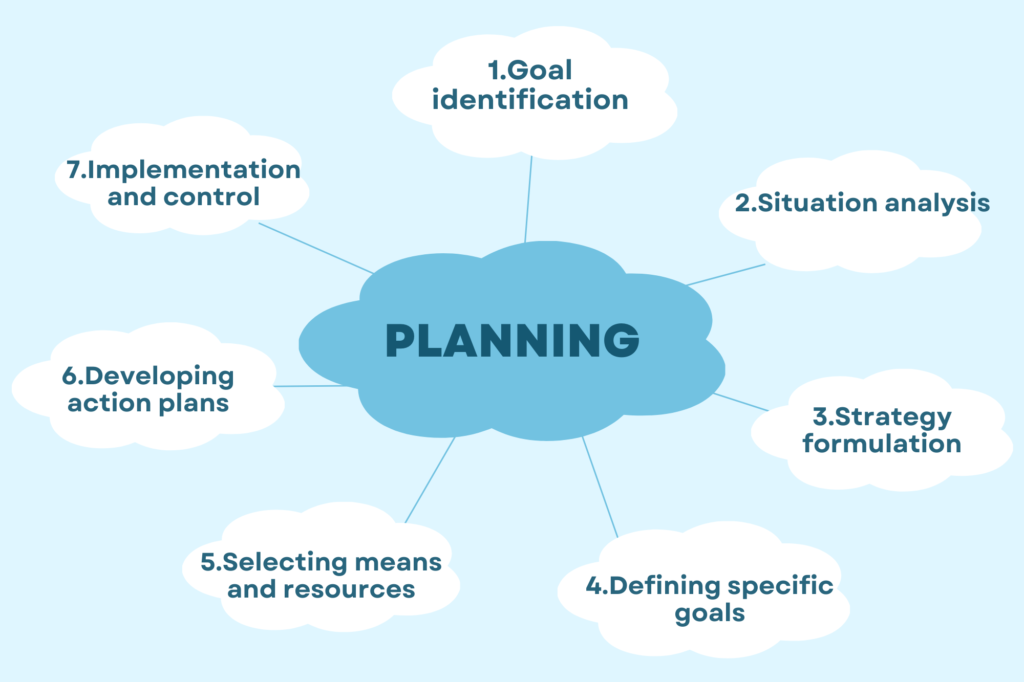
2. Basic planning techniques
- Push – forward planning system
- Pull – backward planning system
- Event-oriented – aligned with just-in-time production principles
The push system – the production orders are executed in a centralized manner. The impulse for production comes from the planning department. The process is “pushed” through individual production stages, and the quantities and deadlines for orders are centrally determined in advance. This approach results in an increase in work-in-progress inventory, and the extended flow time does not guarantee timely task completion. The process is carried out according to a sequentially developed schedule, moving from the first to the last operation. It is characterized by high sensitivity to disruptions, which can arise from changes in completion dates, demand fluctuations, or failure to produce in the intended quantities. In push systems, disruptions are amplified during the execution of successive production phases.
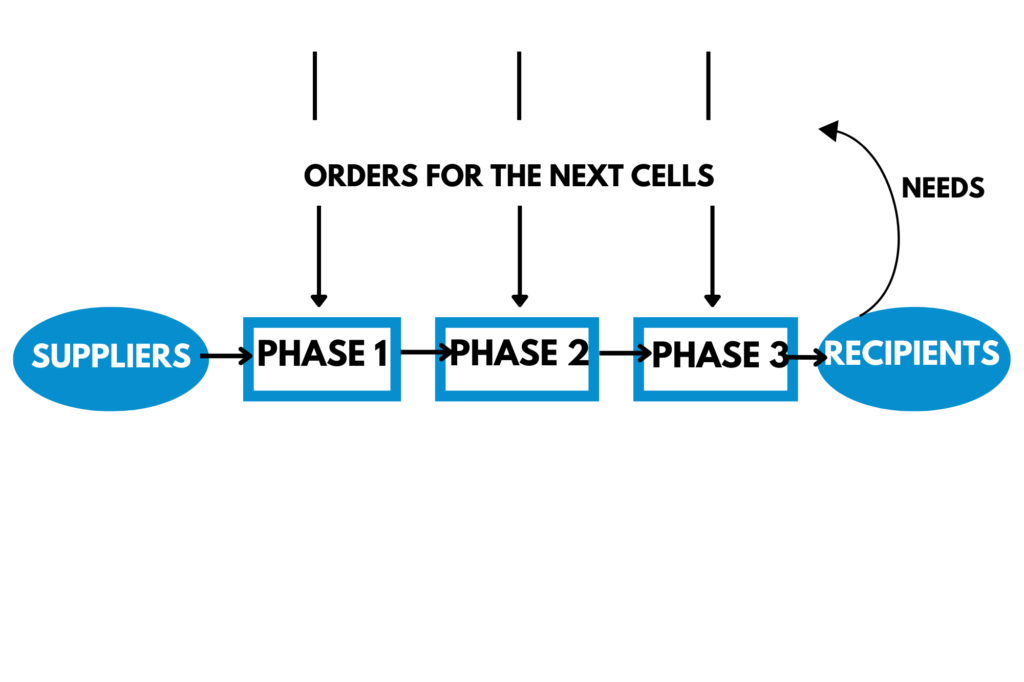
The pull system – the quantities of orders for the preceding production stages are based on the actual demand signaled by the remaining production cells. There is no central order. It relies on predicting the date of shipment of the finished product to the customer, then planning the timing of preceding operations. Disruptions in pull systems are dampened. It is easier to respond to changes in demand, production cycles are shorter, and work-in-progress inventory is smaller.
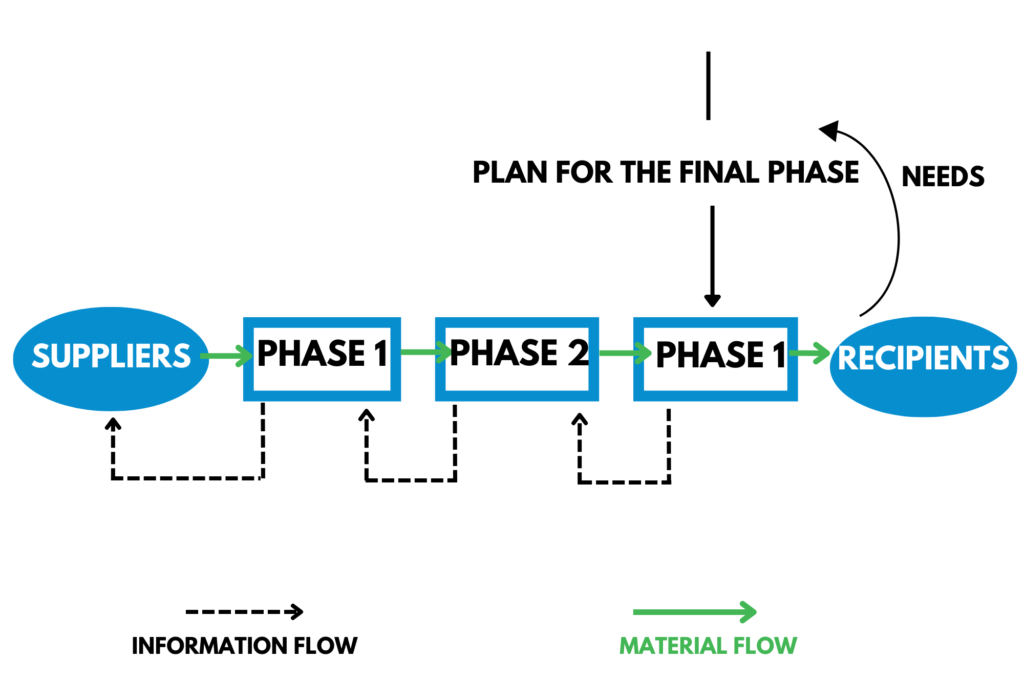
Event-oriented JIT planning – ensures production at the highest level, on time, and at the lowest possible cost. It aims for manufacturing excellence by eliminating waste: “zero defects, zero inventory, zero breakdowns.”
3. Types of pull planning
KANBAN states that production occurs only when demand is signaled, even if it means the idleness of workers or engaging them in other activities such as machine cleaning or quality circles.
KANBAN Motto: “Find a buyer and produce according to their wishes.”
Production planning should consider the details of its implementation, control under the conditions of simultaneous production of other products, and existing resource constraints of the system.
It is one of the more popular pull systems and was implemented by Toyota. Production volume and assortment are planned based on actual sales rather than demand forecasts. The preceding station produces only as many products as needed at the next station. The creation of finished goods inventory leads to an immediate halt in production. The driving force of the system is product demand. Production control is achieved by maintaining a certain level of inventory in between workstations.
CONWIP is a system similar to the KANBAN philosophy but ensures an even lower level of inventory. Its strategy involves maintaining empty inventories in the system, except for the finished goods inventory. The inventory located between workstations only fills up in case of a disturbance at the resource following it. It is emptied after the removal of the disturbance.
KANBAN and CONWIP systems demonstrate their advantages only when applied to repetitive production in relatively large time intervals when orders regarding quantity and assortment change only to a limited extent. They also require stable cooperation with suppliers of input elements for manufacturing. They only allow minor deviations in the load variations compared to the planned values.
4. Types of event-oriented planning
Just-In-Time – is characterized by:
- Eliminating all the waste that occurs during production.
- Looking at the product and predicting future needs and requirements regarding time and quantity, which involves using market research results.
- Precisely predicting the timing of necessary purchases to produce the planned quantity of products at a specific deadline, determined by the customer or resulting from market research.
Principles of Just-In-Time:
- Maintaining an uninterrupted flow of production. The system is driven by demand directly from the customer.
- Simplifying the production system by using more universal or simpler devices that can be quickly and easily retooled. Organizing workstations so that work in progress can be transported according to the production process.
- Arranging purchases for on-demand delivery.
- Improving the efficiency of the manufacturing system.
- Maintaining the required level of quality at each workstation.
- Continuously improving the organization, as it is not possible to completely avoid waste in the system. This is achieved through a gradual process of improving efficiency, reducing defects, and synchronizing production in progress.
TOC (Theory of Constraints) is a concept that converges with JIT. Every system has at least one constraint that prevents it from being perfect. Resources that constitute bottlenecks in the system (resources with the highest utilization) are the only ones unable to take on additional tasks. Therefore, to increase the efficiency of the system, instead of avoiding bottlenecks, the goal is to maximize their number. Detecting and utilizing constraints in the system involves synchronizing the work of critical and non-critical resources.
Non-critical resources work to support critical resources. The flow of production determines the relationships between the operation times of resources. The concurrency of processes and different batch sizes cause bottlenecks to constantly change, and the process is regulated accordingly.
OPT (Optimized Production Technique) is a technique based on the synchronizing role of critical resources. It involves balancing flows, not loads, in the production system. The system’s efficiency, measured by the utilization ratio of resources during one cycle, is higher when there are more bottlenecks. It reaches its maximum value when all resources in the system are critical.
OPT principles:
- The system is characterized by flow balancing, not increasing efficiency. The utilization of non-critical resources depends on critical resources.
- Increasing efficiency before the bottleneck does not increase the system’s overall efficiency.
- An hour saved on a critical resource is an hour saved for the entire system.
- An hour saved on a non-critical resource is just an illusion.
- Creating a queue before the bottleneck does not increase the system’s efficiency.
- The transfer batch does not always have to correspond to the production batch.
- Production batches must be variable, not constant.
- The schedule must consider all constraints occurring simultaneously.
5. Summary
Now, knowing the planning methods and their main characteristics, you can choose a system that best suits your requirements. Regardless of the method you use, every planning approach deserves attention. However, we recommend the event-oriented Just-In-Time planning. It is flexible, emphasizes the elimination of waste, and keeps all production inventories at a minimum level. It aims to achieve alignment between demand and production.