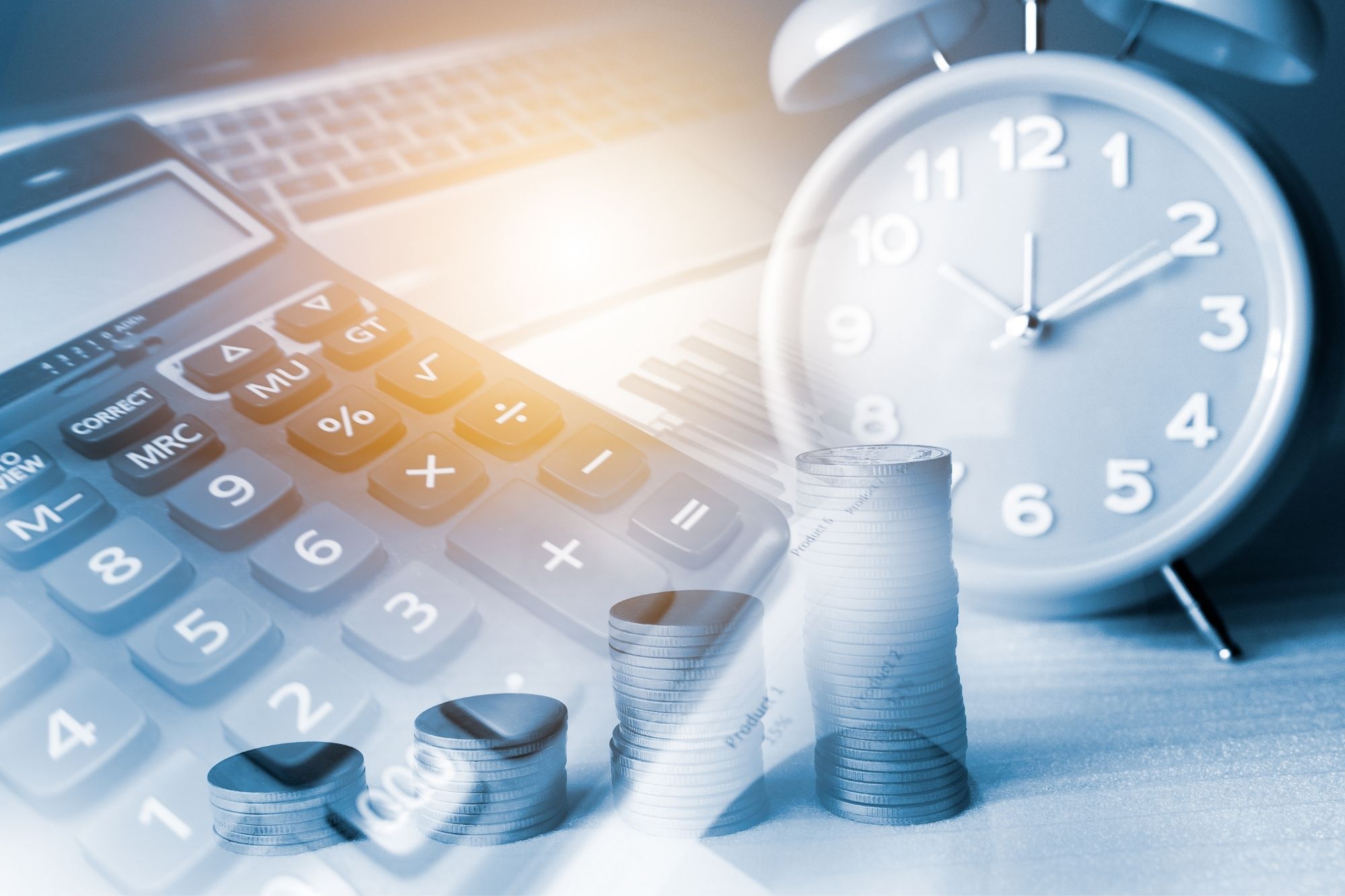
Lean – the key to improved financial health
In a company that is just beginning to implement Lean concepts, the financial results will not change overnight, from month to month, or sometimes even from year to year. This is because it takes time to implement certain processes. Changing the sometimes long-standing habits of the workforce to a new system of operation is very challenging.
However, this is perfectly natural, as people are generally not quick to change their habits. Fear of something new and unfamiliar often inhibits our desire to grow. All these issues are really important, considering the times in which we live. Technology and management systems are developing at an incredible pace which, on the one hand, can be frightening, but on the other, offers a huge number of new opportunities.
Spis treści
1. Elimination of waste
A prosperous enterprise must have skilled employees, robust equipment and use modern solutions. At the end of the day, however, the ultimate and key determinant of a company’s proper health is always its financial performance. It is the numbers that determine the strength of the business, its stability and positive prospects for further growth. Lean Management ultimately aims to improve all economic indicators of the company. The solutions that this management concept proposes lead, among other things, to a reduction in costs and an increase in the productivity of employees and, consequently, the entire company.
The elimination of waste may be clearly associated with cost cutting. However, this concept under the principles of the Lean concept is far more complex. It largely involves looking for and then freeing up time that is consumed in activities that do not add value. This guarantees additional production capacity. The production capacity created by the freed time is intended to finance the company’s growth. Very important in this case is the reassurance of employees that none of them will be laid off as a result of the increased productivity gained through Lean tools. Comfort at work and not having to worry about one’s own position are extremely important for keeping staff productivity at a satisfactory level.
2. What to look out for?
Productivity is the ratio of the result or effect produced by a process to the resources it consumed to achieve that result. Resources in this case are understood as materials, human labor, as well as individual overhead elements. A good knowledge of the productivity of one’s all resources is the first step to improving them. The input parameter is most often human labor, so it is its productivity that is measured first and subjected to the most thorough analysis. It should be borne in mind that the increase in economic indicators of a company cannot be associated only with an increase in productivity. The process is more complex and requires improvement in several aspects. Paying too much attention to productivity can lead to the undesirable phenomenon of overproduction. This is, in the simplest terms, too much product being produced relative to the demand for it. Interestingly, this issue does not necessarily apply only to production, but also to the work of office workers. Too many unnecessary meetings, an excessive number of e-mails sent, unnecessary printing of documentation are also elements that meet the criteria of overproduction. All this generates costs that can be reduced with lean tools.
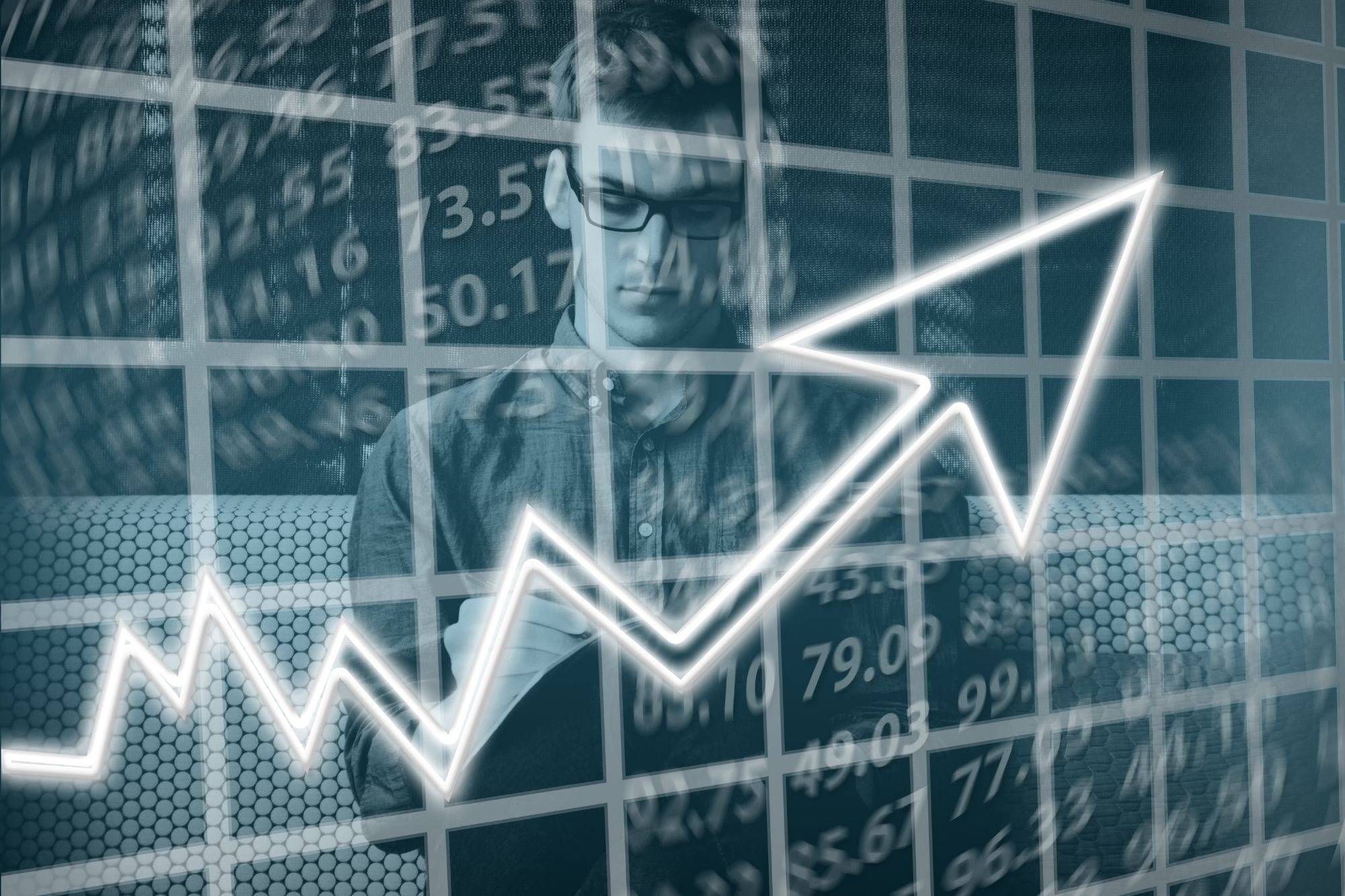
3. What does lean management mean in practice?
The question is – what does the concept of Lean Management really mean in practice? Theory may sound very lofty, but in fact reality verifies practice, that is, what we find in our workplace daily. The first few steps necessary to fully implement lean concepts do not seem complicated. The devil, however, is in the details, which sometimes turn out to have a key impact on the results. The first steps in reducing waste and thus improving the financial health of the company consist of elements such as:
- Orderly and skillful organization of both the office and production halls
- Introduction of task and duty schedule boards
- Ergonomic positioning of common equipment
- Introduction of kanban principles
These are just the first few steps, which on the surface appear to be simple and pleasant to perform, but in reality cause numerous problems. These steps are the nucleus for full optimization of the company’s processes in accordance with the principles of the Lean Management concept.