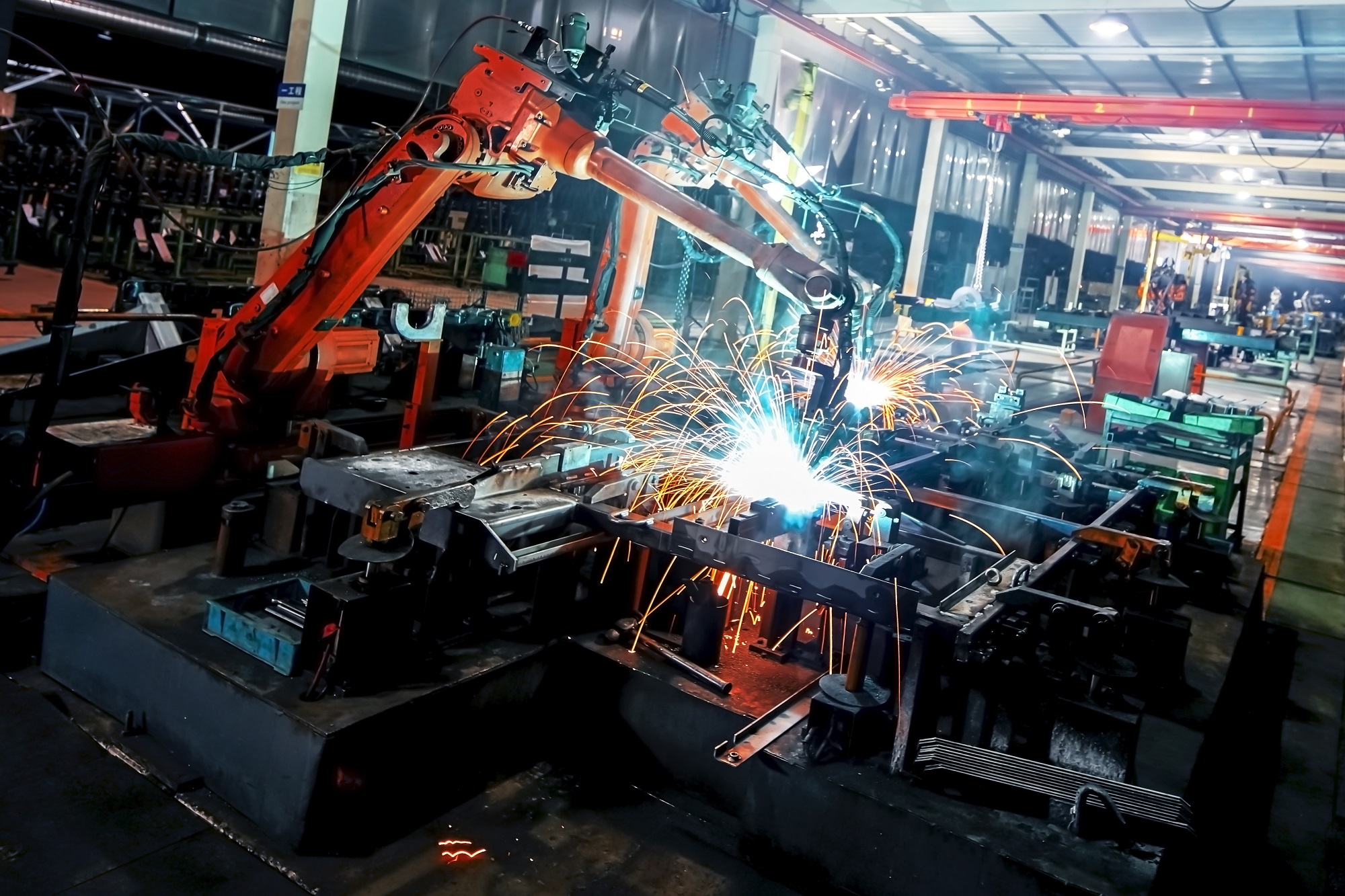
Zautomatyzowane fabryki w Polsce
Automatyzacja procesów produkcyjnych stanowi przyszłość współczesnego przemysłu. Zautomatyzowana fabryka wyposażona w inteligentne roboty to najlepszy sposób na poprawę wskaźników ekonomicznych oraz obniżenie kosztów produkcji całego przedsiębiorstwa.
Spis treści
- Dynamika rozwoju automatyzacji procesów produkcyjnych
- Fabryka Volkswagena w Poznaniu
- Fabryka Fiata w Tychach
- Fabryka Opla w Gliwicach
1. Dynamika rozwoju automatyzacji procesów produkcyjnych
Stale powiększająca się konkurencja sprawia, że automatyzacja procesów produkcyjnych w najbliższych latach będzie coraz dynamiczniej przybierać na sile. Technologia usprawniająca procesy produkcyjne przyszła do Polski z krajów Europy Zachodniej, Stanów Zjednoczonych oraz Japonii. Inżynierowie pochodzący z tych części świata w znacznym stopniu przyczynili się do rozwoju mechanizacji oraz automatyzacji. W Polsce funkcjonują już fabryki wykorzystujące te najnowocześniejsze rozwiązania przemysłowe. W odniesieniu do robotów przemysłowych, zarówno w naszym kraju jak i w innych europejskich państwach, ich największym odbiorcą jest przemysł motoryzacyjny.
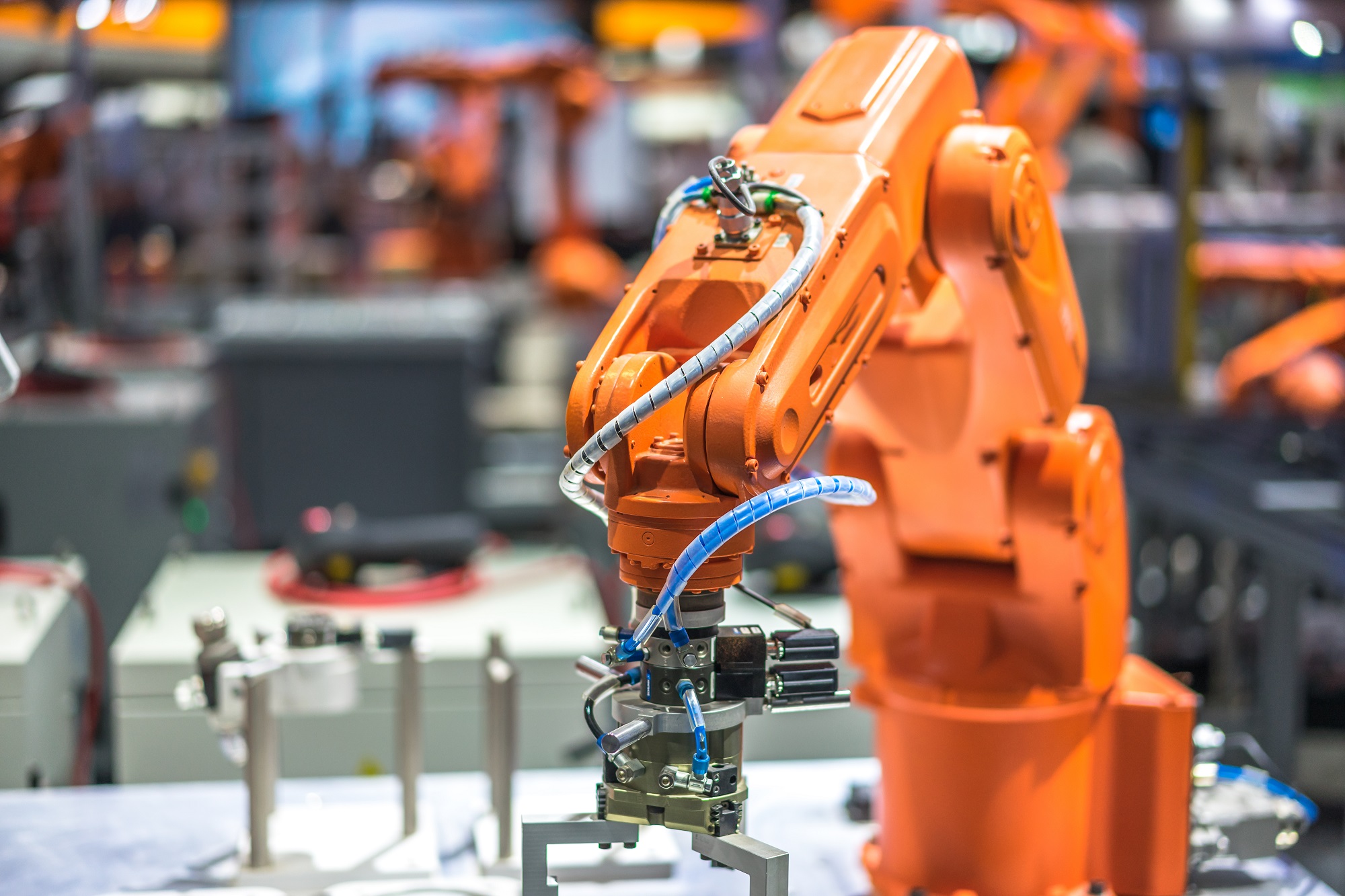
2. Fabryka Volkswagena w Poznaniu
W poznańskim zakładzie produkowane są samochody dostawcze i ciężarowe, a także oparte na wersjach użytkowych samochody osobowe. Fabryka jest również producentem odlewów. Obecnie produkowane tam modele marki Volkswagen to Caddy oraz Transporter. Po trwającej przez ostatnie 2 lata rozbudowie zakładu, większość inwestycji związanych z przygotowaniem do produkcji nowego modelu została niedawno zakończona. Na potrzeby produkcji samochodów najnowszej generacji rozbudowano halę spawalni, a także wybudowano nową halę logistyczną oraz zintegrowano tereny fabryki. Spółka zainwestowała w przeciągu ostatnich lat ponad 2 miliardy złotych na przygotowanie i dostosowanie linii produkcyjnych do budowy kolejnych modeli samochodów. Zainstalowano około 450 nowych robotów, dzięki czemu poziom automatyzacji procesu produkcji karoserii wynosi ponad 80%. Zakład używa między innymi robotów przemysłowych, których producentem jest niemieckie przedsiębiorstwo o nazwie KUKA. Łączenie elementów podwozia odbywa się za pomocą zrobotyzowanego spawania metodą MAG (Metal Active Gas). Od 1 stycznia 2018 roku poznańska fabryka może poszczycić się tym, że jest zasilana w 100% przy wykorzystaniu zielonej energii elektrycznej.
3. Fabryka Fiata w Tychach
Głównym modelem auta wytwarzanym w Tychach jest Fiat 500. Przez ostatnie 14 lat wyprodukowano tu około 2,5 miliona egzemplarzy tego modelu. Fakt ten czyni go najpopularniejszym samochodem w historii tyskiego zakładu produkcyjnego. W 2018 roku fabryka wyprodukowała 259,5 tys. aut, a w 2019 roku 263,2 tys. W roku 2020 nastąpił spadek produkcji na skutek pandemii oraz związanego z nią trzymiesięcznego przestoju wobec spadku popytu na samochody. Fabryka wyprodukowała wtedy 173,9 tys. egzemplarzy. Liczby te czynią zakład jednym z największych z całego koncernu motoryzacyjnego Stellantis. Zdecydowana większość procesu montowania samochodu jest wykonywana przez najnowocześniejsze roboty. Cały proces produkcyjny jednego auta trwa około dwunastu godzin technologicznych. W dziale wtryskarek za pomocą maszyn grupy ENGEL we w pełni zautomatyzowany sposób powstają komponenty wykonane z tworzywa sztucznego.
4. Fabryka Opla w Gliwicach
O budowę najnowocześniejszej na świecie fabryki amerykańskiego koncernu General Motors w latach 90. zeszłego wieku ubiegało się blisko sto miast z całego świata. Ostatecznie podjęto decyzję o budowie fabryki w Gliwicach o czym zadecydowało wiele czynników socjoekonomicznych. Skala inwestycji, a także towarzyszący jej międzynarodowy prestiż przyciągnęły kolejnych inwestorów. Wpłynęło to bardzo pozytywnie na gospodarkę całego regionu. Zakład produkcyjny od samego początku stał się liderem i promotorem rozwiązań z zakresu zarządzania produkcją, innowacyjnością oraz bezpieczeństwem. Początkowo co prawda, wszystko było wykonywane za pomocą ludzkich rąk. Po jakimś czasie na linii produkcyjnej pojawiły się roboty firmy ABB. Ich zadaniem było uszczelnianie podwozia, a pracownicy wykańczali te operacje. Obecnie zakład rozwinął się na tyle, że zarówno podwozie jak i nadwozie aut jest robione praktycznie w całości automatycznie. Fabryka w Gliwicach dzięki nowoczesnej infrastrukturze i technologii stanowi jedną z najlepszych jednostek produkcyjnych spośród całego koncernu General Motors pod względem zużycia energii. Wpływ na to mają także nieustannie wdrażane projekty środowiskowe dotyczące optymalizacji zarządzania energią.